Silicone and EPDM Rubber Tubing : Maintenance and Durability
Maintenance and Durability of EPDM and Silicone Rubber Tubing
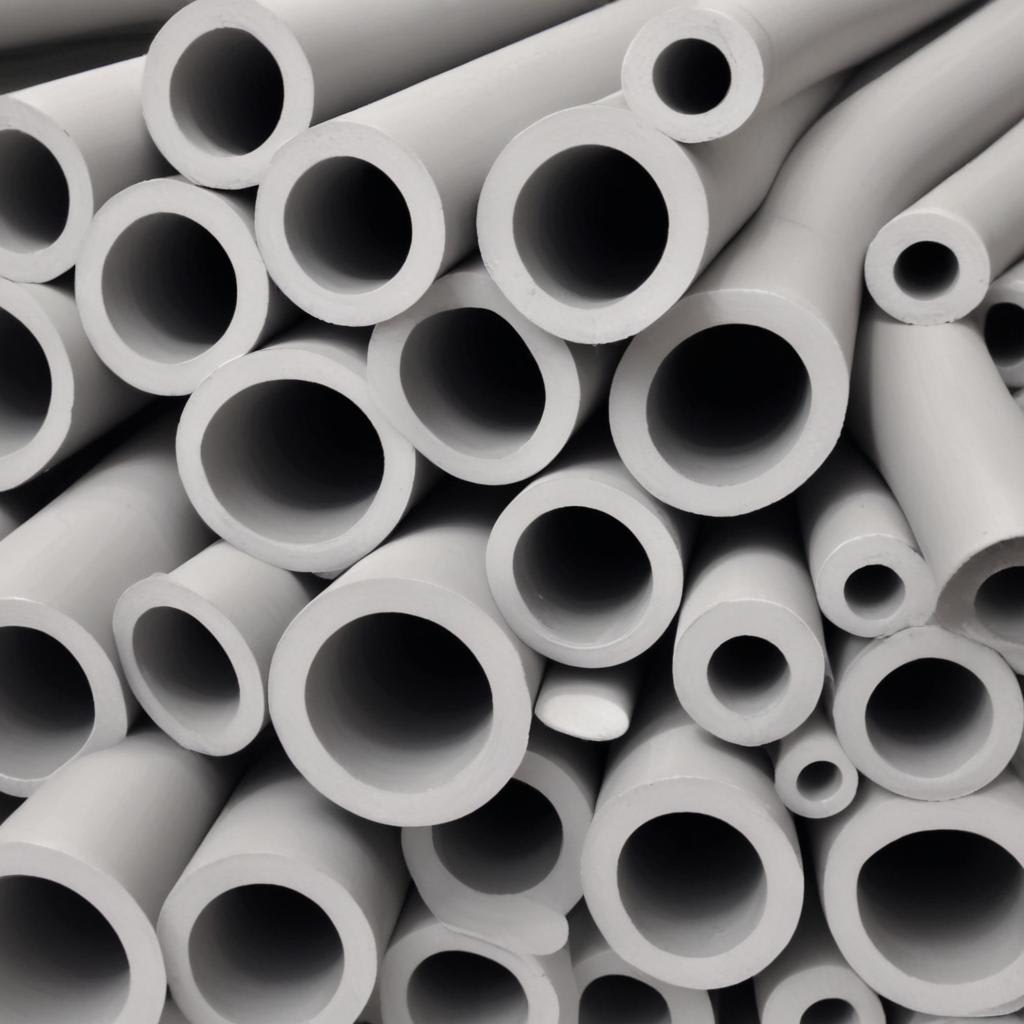
Silicone and EPDM rubber tubing has various applications for use in automotive industries, health care industries, and food and beverage preparation industries. These rubber materials choices are based on their characteristics such as flexibilities; resistance to high and low temperatures; and chemical stability. Yet these tubes can only be useful if they are well maintained so that they can remain as effective as needed for long. That is why this blog will focus on the strategies and the features that define the service life of silicone and EPDM rubber tubing.
Understanding the Properties of Silicone and EPDM Rubber Tubing
Silicone Rubber Tubing:
It is known for its extreme flexibility as well as its ability to perform in environments that are hot or cold with temperatures varying from 60 to 230 degrees Celsius (-76 to 446 degrees Fahrenheit). It also possesses a high degree of stability in the areas of UV radiation and weathering as well as in exposure to ozone. Furthermore, silicone rubber is a chemically stable material, and does not dissolve in various chemical solutions, thus making it ideal for use where hygiene is a critical issue as is the case with medical and food related products.
EPDM Rubber Tubing:
EPDM rubber tubing is known for its heat resistance, oxidation, inertness to ozone, and weather factors. It can cope with negative forty centigrade degree Celsius to one hundred and fifty centigrade degree Celsius (-40 F to 302 F). EPDM is also highly resistant to water and steam hence its use commonly in automotive applications and heating ventilation and air conditioning industries. Still, EPDM is not compatible with oils, gasoline, and any product that contains hydrocarbon in its composition.
Factors Affecting the Durability of Rubber Tubing
Several factors can influence the durability and performance of silicone and EPDM rubber tubing:
1. Temperature Exposure:
Silicone and EPDM rubber tubing are used in applications that require parts to be resistant to a large variety of temperatures. But they lose their flexibility and strength when they are exposed for too long to either hot or cold temperatures. One must make sure the tubing is used at recommended temperature not to reduce its longevity It is recommended to ensure that the tubing used is within the require temperature limit for its effective use.
2. Chemical Exposure:
Although silicone rubber has very good resistance to chemical attack, EPDM rubber is relatively more selective about it. Even when the tubing and fluids are chemically compatible, exposure to incompatible chemicals may lead to swelling, hardening, or crack formation. Tubing chemical compatibility is recognized to be an important aspect and therefore the chemicals that the tubing will be in contact with must be determined and matching material selected.
3. UV and Ozone Exposure:
Silicone tube has ability of sealed UV light and ozone resistance features while EPDM rubber tubing also exhibits features of sealed UV light and ozone resistance. Nevertheless, wearing fades gradually when one continually attends the scrappy environment filled with such elements. These effects can be reduced by using of the protective coatings or UV resistant grades of the tubing.
4. Mechanical Stress:
Rubber tubing may easily breakdown whenever they are subjected to frequency bending stretching or even compressing. Prevention from mechanical stress is also another way of ensuring that the tubing in question is in the right state. To extend the tubing’s life, proper installation must also take place whereas it is advisable not to produce sharp bends or twists at any point.
5. Abrasion:
The tubing can degrade due to rubbing against roughly surfaced objects and particles that are hard on the tubing. To reduce the effects of abrasion, one can wear abrasion-resistant sleeves or apply protective coatings to the equipment.
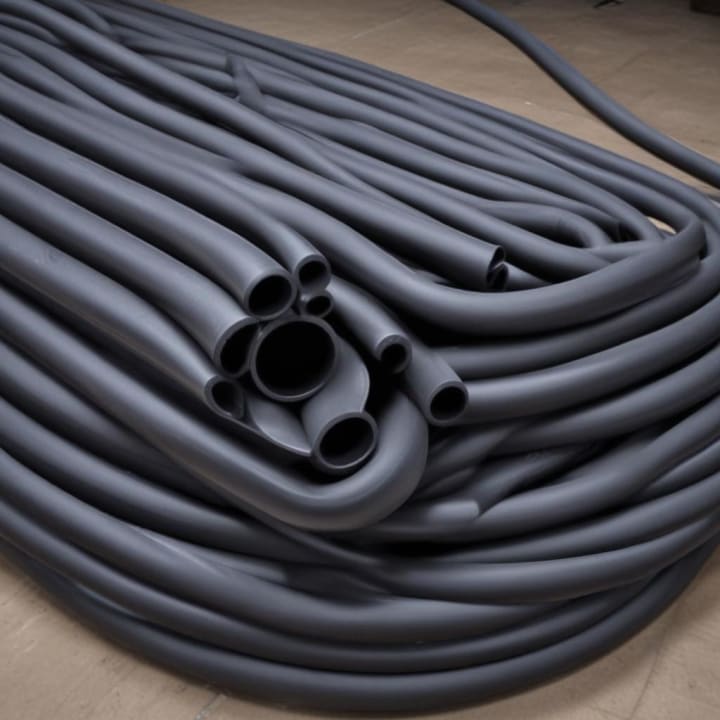
Best Practices for Maintaining Silicone and EPDM Rubber Tubing
1. Regular Inspection:
Before use, rubber tubing should be inspected for any signs of wear, damage, or degradation by routinely checking on it. Specific features of the exterior paint are that it can peel, crack , swell, harden, or become discolored. The failure of the tubing can be prevented or it can be detected early hence avoiding a lot of down time.
2. Cleaning:
It is very important for the rubber tubing to be clean to ensure that there is no accumulation of different interferences that may lead to degradation. For silicone rubber tubing, it is best to clean it with mild soap and water and should not use abrasive cleaners because it may harm the surface. EPDM rubber tubing may be washed with mild soaps and detergents under no circumstances should it be scrubbed. It is important that whatever tubing is used should be cleaned well and then washed and dried before being used again.
3. Proper Storage:
To prolong its life rubber tubing should be kept in a cool and dry environment and away from direct sunlight, ozone producing devices such as electric motors. One should refrain from stacking or folding the tubing in tightly coiled formations so as to result in kinking of the tubing. Prolonged exposure may damage the tubing, so if possible, one should retain the manufactures pack for protection against these factors.
4. Avoiding Overloading:
It should not be exposed to pressures or loaded beyond its capacities as recommended by the manufacture. Overloading may result into bursting of the tubing or reach its designed life cycle much earlier. Select fittings and clamps that appropriately fit the tubing to avoid placing too much pressure on it.
5. Using Protective Coatings:
The application of protective coatings can help increase how long rubber tubing will last. For instance, to avoid damage from sun exposure, there are UV resistant coatings available that could be applied to the tubing; similar, for use with hard surfaced items, there are abrasion resistant coatings available. To avoid any problems, refer to the manufacturer for the suitable coatings which are compatible with the said tubing.
6. Proper Installation:
Before vigorously utilizing rubber tubing, it is strongly advised that one should correctly install this device. It is also important to note that during its installment do not bend frequently, twist or make kinks in it. Select proper fittings and connectors for getting a good seal and no leakage issues. It is imperative to adhere to the instructions issued by the manufacturer for the procedures of installation.
Extending the Lifespan of Rubber Tubing
To maximize the lifespan of silicone and EPDM rubber tubing, consider the following additional tips:
1. Monitoring Operating Conditions:
Frequency of the monitoring of the operating conditions such as temperature, pressure, and hazardous chemicals. Make sure that usage of the tubing is within BHP’s set parameters on using the equipment. In case the conditions that surround the tubing change, retests the compatibility of material for the new conditions.
2. Preventing Contamination:
This means that contaminants can hasten the destruction of the rubber tubing. The particles should not get into tubing; filters and strainers should be used to avoid this. In the situations where two or more agents are in contact with the structure, guarantee that these agents are fluids with no contaminants.
3. Replacement Schedule:
Develop a schedule to replace the tubing following the life expectancy timelines and the working environment. Preventive replacement of tubing is more advantageous than having a system fail and then replace the tubing because it has worn out.
4. Training and Education:
Train personnel on the use of rubber tubing; its proper handling, care and how to conduct regular check-ups on it. Make sure they know the factors that causes changes in the behaviors of the tubing and the relevant procedures to follow.
Conclusion
Silicone and EPDM rubber tubing are essential for use in differing contexts because of their distinctive characteristics to fit the various industries. The main idea that is connected with them is that they are reliable if properly maintained. Once you learn the causes of poor efficiency in the rubber tubing used and where to source the best ones around you, then you shall be able to select the best quality tubing to use and on how to maintain them so that they can serve you for longer time. Some of the measures that one can take in order to maintain the efficiency of the silicone and EPDM rubber tubing include; taking regular inspections on the tubing, proper cleaning of the products especially before they are used and careful installation among other measures.
About the Creator
Enjoyed the story? Support the Creator.
Subscribe for free to receive all their stories in your feed. You could also pledge your support or give them a one-off tip, letting them know you appreciate their work.
Comments
There are no comments for this story
Be the first to respond and start the conversation.